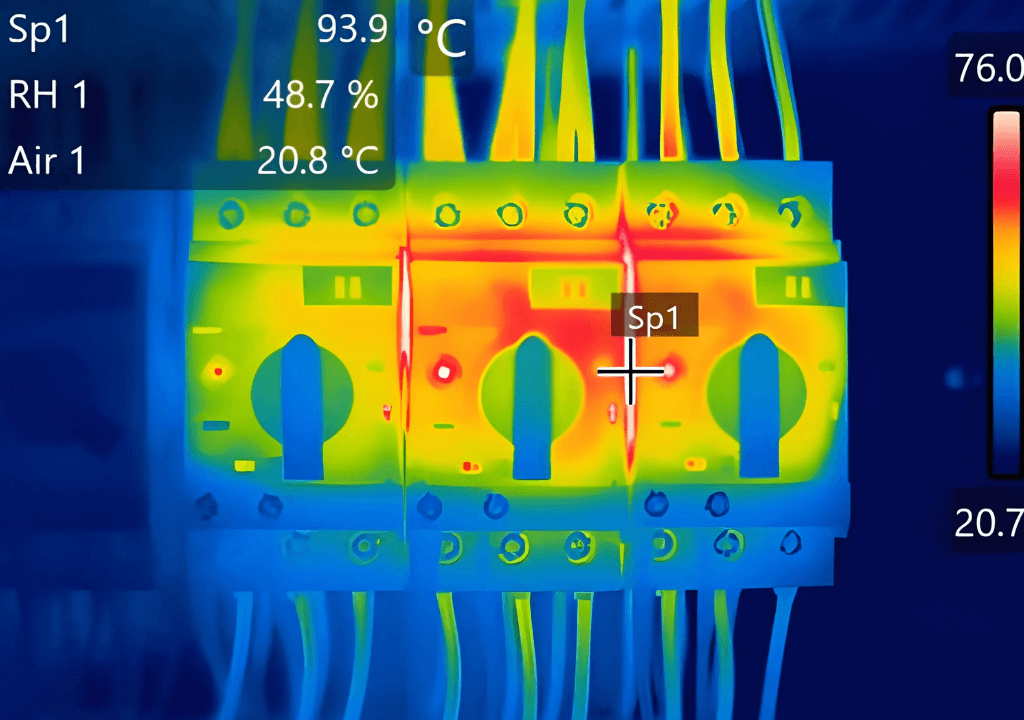
Electrical Thermal Imaging – Detecting Potential Hazards Before They Escalate
Electrical systems are complex, and undetected faults can lead to significant damage, safety risks, or costly downtime. This is where electrical thermal imaging comes in – it’s a proactive, non-invasive tool that helps us spot potential electrical problems you can’t see with the naked eye. By using special infrared cameras, we can pinpoint hot spots, overloads, and other hidden issues in your electrical systems. This allows us to address them before they escalate into serious problems like fires, equipment failure, or expensive repairs.
At Test And Tag Kiwi, we provide comprehensive electrical thermal imaging services to keep your electrical systems safe, efficient, and reliable, whether you’re in a residential, commercial, or industrial setting. We also offer a range of other essential electrical safety services, including:
Free Quick Quote
What Exactly is Electrical Thermal Imaging?
Electrical thermal imaging uses infrared cameras to capture thermal images (also called thermograms) of your electrical components and systems. These images display temperature variations using different colors, making it easy for our technicians to identify areas that are overheating or under stress. Hotspots can signal underlying issues like poor connections, circuit overloads, insulation breakdowns, or failing electrical components.
This method is non-destructive and non-invasive, making it perfect for ongoing preventative maintenance and safety inspections without needing to shut down your systems or perform invasive procedures.
Why is Electrical Thermal Imaging So Important?
- Catch Hotspots Early: One of the biggest advantages of thermal imaging is its ability to find hotspots in electrical circuits. Overheating can be caused by weak connections, damaged cables, or excessive current. If left unchecked, these hotspots can lead to electrical fires, equipment failures, and costly repairs. Thermal imaging helps us pinpoint these issues early, allowing for precise repairs.
- Prevent Equipment Breakdowns: Over time, electrical components like transformers, circuit breakers, and wiring can wear out. Thermal imaging helps us detect the early signs of stress or failure in equipment before it leads to significant downtime, damage, or expensive fixes.
- Boost Electrical System Efficiency: By identifying areas where electrical components are running inefficiently (like unnecessary heat buildup), thermal imaging can help optimize your electrical system. This can lead to better energy efficiency, lower operational costs, and a more reliable electrical setup.
- Non-Invasive and Non-Destructive: Unlike traditional diagnostic methods that often require shutting down equipment or disassembling parts, thermal imaging is non-invasive. We can perform scans while your equipment is running, minimizing disruptions to your operations. This makes it an ideal tool for regular maintenance and inspections without causing downtime.
- Early Fire Hazard Detection: Overheating electrical connections, overloaded circuits, or faulty equipment can pose a serious fire risk. Electrical thermal imaging allows you to identify these potential hazards before they escalate, ensuring your system remains safe and compliant with fire safety regulations.
- Compliance and Risk Management: Regular thermal imaging scans help businesses meet occupational health and safety regulations and industry standards. It also aids in managing risks associated with electrical systems by providing early detection of faults that could cause safety concerns.
Our Electrical Thermal Imaging Process
At Test And Tag Kiwi, we use advanced infrared cameras and diagnostic tools to provide accurate and reliable electrical thermal imaging services. Here’s what you can expect:
- Pre-Survey Assessment: We start with a visual inspection of your electrical systems and components. This helps us identify areas that might need a closer look with thermal imaging. We’ll also discuss any specific concerns you have, such as frequent electrical faults, tripped circuit breakers, or power surges.
- Thermal Imaging Scan: Using our cutting-edge infrared cameras, we scan electrical panels, circuit breakers, switchboards, transformers, wiring, and other electrical components. The camera detects heat emissions and creates thermal images that clearly show abnormal temperature patterns. These images are color-coded, making it simple to spot potential problems.
- Identifying Potential Problems: The thermal images help us identify issues such as:
- Overheated connections or conductors
- Faulty or worn-out electrical components (e.g., circuit breakers, fuses, switches)
- Electrical overloads or imbalances
- Insulation breakdowns or deteriorating wiring
- Hot spots in transformers or switchgear
- Analysis and Reporting: After the scan, we thoroughly analyze the results. Our experienced technicians will assess any hotspots, irregularities, or potential faults and determine their root causes. We then compile a comprehensive report that includes the thermal images, identified issues, recommendations for repairs or maintenance, and a suggested timeline for addressing the problems.
- Follow-Up and Maintenance: If we find any critical issues, we’ll provide immediate recommendations for corrective actions, such as tightening connections, replacing faulty components, or improving system design. We also offer ongoing maintenance plans to ensure your electrical system continues to perform efficiently and safely.
- Documentation: For compliance and audit purposes, we provide detailed documentation that includes a summary of the thermal imaging inspection, a record of the equipment scanned, and any required repairs or maintenance. This helps you maintain a clear record of electrical safety inspections for future reference.
Benefits of Electrical Thermal Imaging
- Early Detection of Potential Hazards: Catching potential faults or failures early prevents more serious issues like electrical fires or major equipment breakdowns.
- Increased Safety: Identifying hotspots and faulty components helps prevent electrical accidents, reduce fire risks, and ensure the safety of your home, office, or facility.
- Cost Savings: Early identification of issues can help you avoid costly repairs, replacements, or downtime caused by undetected faults. Regular thermal imaging inspections help you maintain an efficient and cost-effective electrical system.
- Operational Efficiency: By identifying and addressing inefficiencies, you can improve your electrical system’s overall performance, saving energy and reducing long-term operational costs.
- Minimized Downtime: Thermal imaging allows inspections to be carried out without needing to shut down equipment, minimizing downtime and disruption to operations.
- Compliance with Regulations: Regular thermal imaging is often a requirement for regulatory compliance, especially in high-risk industries like manufacturing, construction, and commercial facilities. It helps ensure your electrical systems meet safety standards and regulations.
Common Electrical Issues Detected by Thermal Imaging
- Overloaded Circuits: Areas where electrical circuits are overloaded will appear as hotspots in thermal images. Overloaded circuits can lead to fires, equipment failure, and power outages.
- Loose or Corroded Connections: Loose or corroded electrical connections create resistance and heat buildup, which can cause electrical fires. These issues are easily detected by thermal imaging.
- Short Circuits or Faulty Wiring: Short circuits often result in excessive heat buildup in specific areas. Thermal imaging helps locate these faults quickly.
- Overheating Components: Electrical components like transformers, motors, or circuit breakers that are overheating can be identified before they fail, preventing costly damage and downtime.
- Inadequate Insulation: Poorly insulated cables or components can create heat imbalances, which are easily detected by infrared cameras.
Why Choose Us for Electrical Thermal Imaging?
- Experienced Technicians: Our team is highly trained in using infrared thermography equipment to provide accurate, reliable assessments of your electrical systems.
- Advanced Technology: We use the latest infrared cameras and diagnostic tools to ensure precision and efficiency in detecting potential electrical faults.
- Comprehensive Reports: We provide detailed thermal imaging reports that include high-quality images, identified issues, and actionable recommendations for repairs or maintenance.
- Non-Disruptive Service: Our thermal imaging service is non-invasive, meaning we can perform inspections without shutting down your operations or disrupting your daily activities.
- Affordable and Reliable: We offer competitive pricing for high-quality thermal imaging services, ensuring you receive the best value for your investment in electrical safety and efficiency.
Contact Us for Electrical Thermal Imaging
Ensure the safety, reliability, and efficiency of your electrical systems by scheduling a thermal imaging inspection with Test And Tag Kiwi. Our expert technicians will provide a detailed analysis and help you address potential risks before they become serious issues.
Contact us today to learn more about our electrical thermal imaging services or to book an appointment!