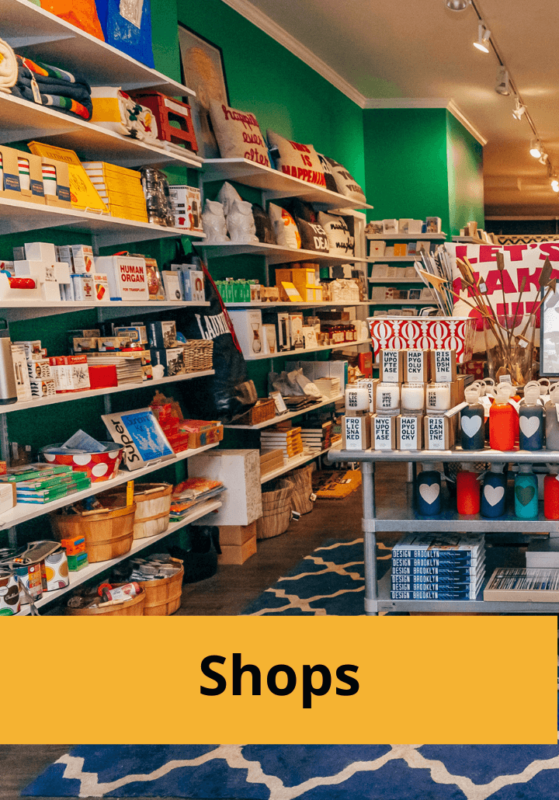
Factory Sites
Powering Safety and Productivity
In the dynamic environment of a factory, electrical equipment is the lifeblood of production. From heavy machinery to power tools and lighting, every electrical item must operate reliably and, above all, safely. This is where dedicated Test and Tag services become an integral component of operational efficiency and risk management for any factory site.
At Test and Tag Kiwi, we understand the rigorous demands and diverse range of electrical equipment found within manufacturing and industrial facilities. Our comprehensive electrical testing and portable appliance testing for factories are designed to uphold the highest safety standards, ensuring continuous operation and protecting your most valuable assets: your people and your plant.
Our appliance test and tag procedures are carried out by skilled technicians who are adept at navigating active factory floors. We meticulously inspect and test a vast array of electrical items, adhering strictly to New Zealand’s Electricity (Safety) Regulations 2010 and the AS/NZS 3760:2022 standard for in-service safety inspection and testing of electrical equipment. This ensures every piece of portable electrical equipment meets the required safety benchmarks.
We pride ourselves on providing efficient test & tag services that minimise disruption to your production schedule. Our team can work flexibly around your operations, ensuring compliance without impacting your output. We provide detailed reports of all tested equipment, offering clear documentation for your safety records and audits.
For robust test and tag Auckland services that empower your factory with superior electrical safety and contribute to seamless production, partner with Test and Tag Kiwi. Let us help you maintain a compliant, safe, and highly productive working environment.
Our Tailored Test and Tag Services for Factories Include
As leading providers of Auckland test and tag solutions, our services are specifically adapted to the unique challenges of industrial settings. We cover:
- Power Tools: Drills, grinders, saws, and other hand-held portable tools critical for fabrication and assembly.
- Workshop Equipment: Bench grinders, portable welders, air compressors, and other portable machinery.
- Production Line Appliances: Any portable electrical components, control units, or ancillary equipment that supports manufacturing processes.
- Cleaning & Maintenance Gear: Industrial vacuum cleaners, floor scrubbers, and other portable maintenance tools.
- Office & Amenities Equipment: Computers, printers, microwaves, and kettles found in administrative offices, staff rooms, and break areas.
- Extension Leads and Power Boards: Essential for flexible power distribution across the factory floor, these are meticulously inspected and tested due to their high usage.
- Single phase testing: Applied to the vast majority of portable electrical items commonly found in factory environments.
- Portable RCDs (Residual Current Devices): Crucial safety devices that require regular testing to ensure they trip quickly in the event of an electrical fault, protecting workers from electric shock.